Innovation Unveiled: Cutting Edge Technologies in Printed Tape Manufacturing
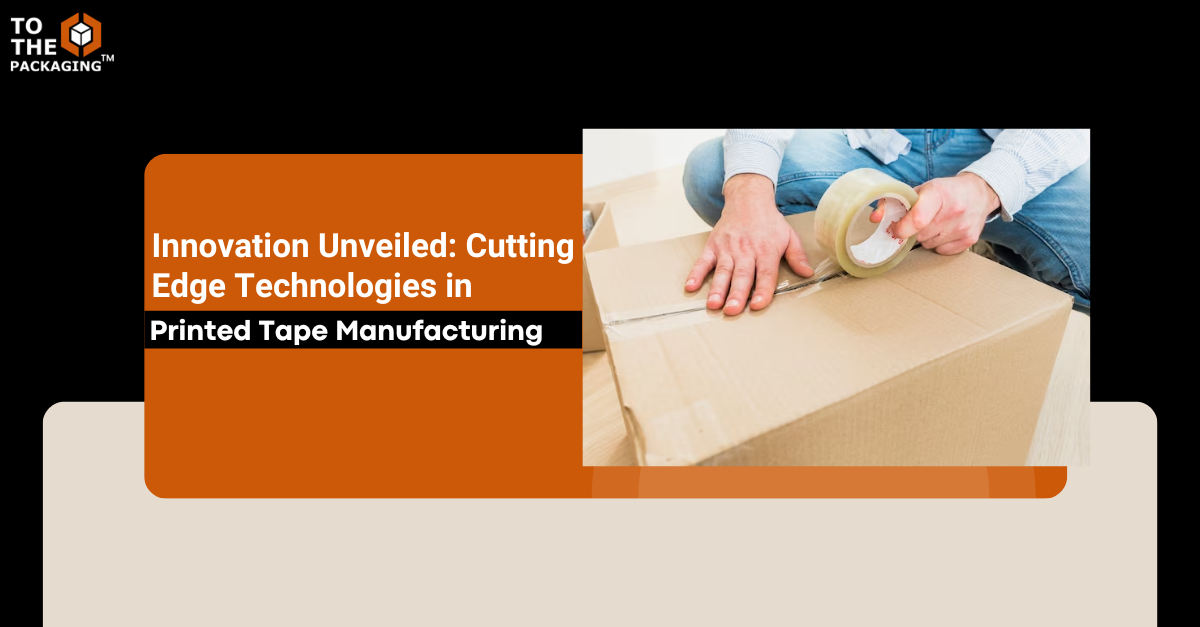
Printed tape serves as a powerful branding tool. So, printing on tape has become very common for businesses. They add logos and branding elements on packaging tapes to promote their brands. Advancements in printing technology have enhanced the clarity and quality of printed tapes. Various technologies are used in printed tape manufacturing to improve printed tapes' visual appeal and functionality. What are the printing techniques used?
Printing techniques
1. Rotogravure printing
Rotogravure printing is also called gravure printing. It is a high-quality printing process. The process involves the application of ink to a substrate with a copper or chrome metal plate on an engraved cylinder. In this technique, the text or image to be printed is engraved onto the metal plate. Using the impression increases color vibrancy in the print and assures precise results. The plate is mounted on a rotating cylinder and transfers the design to the tape substrate.
Pros
- Quality is its biggest plus. Its image reproduction, fine details, and vibrant colors make it an excellent choice for high-quality printing.
- Gravure printing is ideal for large-quality production because it is a fast process.
- You are assured of consistency throughout the printing process.
- It is suitable for special effects like embossing.
Cons
- It is expensive. The initial investment in equipment is costly. So it is not suitable for small-scale production.
- The inks you use for gravure printing are solvent-based inks that are not environment-friendly.
- Color control is not accurate in this type of printing.
2. Flexographic printing
It is a high-speed printing process commonly used for printing labels in bulk. Flexographic printing is used to print tapes, gift wraps, bags, envelopes, cartons, disposable plates, and cups. The first step in this process is to create printing plates. Then ink is transferred to the printing roller. The text and graphic design are raised from the surface and ink is applied on the raised parts. It is known for its high-quality printing.
Pros
- It is a fast and quick process. Its high-speed production makes it a good choice for packaging. The ink dries up fast. So, it transfers images on the tapes rapidly.
- Flexo printing is ideal for printing on rough surfaces.
- The printing stays for a longer time. Its durability is a big advantage. You can print in large quantities and store them.
- The initial setup cost is high but it can create millions of impressions. So, it is cost-effective.
- It is environment-friendly because water-based ink is used.
Cons
- The print quality is not up to the mark.
- It is not a smart choice for small and limited printing.
3. Digital printing
Digital printing has gained a lot of popularity these days because of its cost-effectiveness and versatility. It uses modern techniques like laser printing and inkjet printing. There is no need for plates or cylinders in this type of printing. So, setting up is easy and quick. Moreover, it provides high-resolution printing. This makes it suitable for printing small text, complex graphics, and intricate designs.
Pros
- Digital printing is fast and efficient with quick turnaround.
- It is ideal for small businesses because it is cost-efficient to print smaller quantities. It is the best choice for limited edition tapes.
- You can add printed protection using digital printing. This enhances the security of your package.
- Laser digital printing helps to engrave texts and images that are difficult to forge, helping to avoid counterfeits.
- You can fit any design in digital printing which helps to reduce wastage.
Cons
- The color output may not be the same. It may vary from run to run and printer to printer. So, you cannot expect the same results for repeat orders.
- Ink options are limited in digital printing.
4. Sandwich printing
In this printing technique, printing is made between the adhesive and tape. That is why it is called sandwich printing. The print between the foil and the adhesive cannot be deleted. It takes a longer time than the classic printing. It may take from 4 to 6 weeks. Moreover, it is printed in large batches starting from 600 mm in width. The minimum number of tapes is 450 pieces approximately. In this technology, you can choose up to 6 colors.
Pros
- It is suitable for medium and large quantities.
- If you are looking for high quality, this is a good option.
Cons
- It is not suitable for small quantities.
- The production process is complex and takes a long time.
5. Direct thermal printing
This technique works by applying direct heat on the material. There are no inks, ribbons, or toners. It needs a special type of heat-sensitive material that blackens when heat is applied.
Pros
- The printers are easy to operate, compact, and need less maintenance.
- The ribbon-free mechanism is simple.
Cons
- It is not the best choice for long-term use because the print fades in less than six months.
- The prints are sensitive to chemicals, sunlight, water, and abrasions.
6. Thermal transfer printing
This technique uses ribbons made of resin or wax that melt into the surface and create a long-lasting image. You can use thermal printing on a wide array of materials including paper, plastic, and fabric. You can use colored ribbons to create color-coded tapes.
Pros
- It is long-lasting and is not affected by light, chemicals, and water.
- It is the best option for cold storage.
Cons
- It is slightly expensive.
7. Inkjet printing
In this method, tiny droplets of ink are sprayed directly over the surface.
Pros
- It handles high-resolution images efficiently.
- It allows for variable printing.
Cons
- The durability of the print depends on the type of ink.
- The cost is higher for large volumes.
Conclusion
The custom-printed tape makes the first impression. So, you should choose the right printing type for your packaging tapes. While choosing the printing technique for your printed tape, you should consider factors like the volume of packaging, print quality, budget, etc. Make sure the technique is compatible with your requirements.

To The Packaging, is a firm with more than 20 years of experience in the packaging business. We believe in creating innovative solutions for all kinds of packaging problems for big and small businesses.